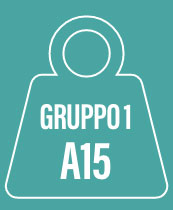
MINIMAL RESISTANCE LOAD > 15 kN
Exclusively pedestrian and cycling areas.
As per EN 124:2015, the production process of our manholes covers falls under class C2 (“Composite material C2” Point 4.2 Type of composite materials). This is a compression molding process made with a closed mold under controlled temperature (SMC) that employs thermosetting resins (polyester resin), short glass fibers (chopped strand) and other additives. The production process guarantees excellent fibers’ wettability from the polymer matrix. Moreover, it avoids air bubbles and creates an excellent interlaminar cohesion between components.
Our FRP manholes covers are designed to meet A15/B125/C250/D400 load ratings’ requirements in accordance with EN 124:2015. Moreover, FRP covers have hardness characteristics similar to cast iron ones, while having better resistance to residual strains.
Exclusively pedestrian and cycling areas.
Sidewalks, pedestrian or similar areas, rest areas and car parking garage.
Areas of drainage channels along the sidewalks that run for a maximum of 0,5m onto the roadway and for a maximum of 0,2m onto the sidewalk.
Roadways (including pedestrian ways), transitable platforms and rest areas for road vehicles of all kinds.
Design requirements, type testing, markings, quality checks according to EN 124:2015. Certification issued by ICMQ.